Posted on over 3 years ago by Laurentina Kennedy
How to continue to lure biopharma FDI to Ireland
World-class advanced manufacturing key as Factory 5.0 standard succeeds Industry 4.0
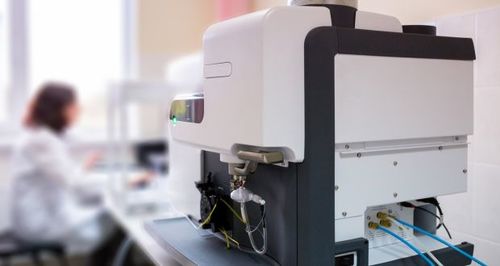
A new front is emerging in the global battle for biopharmaceutical foreign direct investment. With the OECD agreement on a global minimum tax rate effectively done and dusted and talent becoming increasingly mobile in the wake of the Covid pandemic, countries now have to look to other competitive differentiators as they seek to attract the next wave of biopharma investments.
Chief among these will be the ability to offer world-class advanced manufacturing environments and capabilities. And, in that respect, Industry 4.0 is already being superseded with best-in-class companies and facilities now setting their sights on the Factory 5.0 standard.
Biopharmachem Ireland, the Ibec division which represents the biopharma and chemical sectors, is co-ordinating a new initiative to help transition the industry in Ireland to this new and more sustainable model.
“Factory 5.0 is the successor to Industry 4.0,” says Biopharmachem Ireland director Matt Moran. “It has everything that Industry 4.0 has and combines it with sustainability, a reduced carbon footprint, and ensures that employees are looked after and involved in the process. It is more human-centred. We’ve been working on the project for about a year if not longer. It is led by Johnson & Johnson and supported by the IDA. We are looking initially at the active pharmaceutical ingredient (API) sector, the more traditional part of the industry in Ireland. This is where it all started with companies like Pfizer and MSD and so on.”
Maturity assessment
A cluster of firms including Pfizer, MSD, Lily, Merk and Johnson & Johnson have come together to progress the project. “We have also brought in some contract manufacturers as well as some tech companies like Analog and Siemens,” says Moran. “We want to explore the crossover between the technology and biopharma industries.”
The project has now reached a stage where a maturity assessment of the companies is being carried out to benchmark them against Factory 5.0. “Innopharma, an advanced manufacturing training specialist with particular expertise in the biopharma industry, is assessing the companies to see where they are on the roadmap. What we are trying to do is build an ecosystem of digitalised companies and then add suppliers, engineering companies, academic researchers, State agencies, research centres and so on. We will ultimately spin that out to the rest of the industry and bring it to a European platform.”
According to Moran, the initiative was prompted at least in part by Covid and the massive supply chain disruptions it created. “Companies are looking at nearshoring and reshoring supply sourcing for chemicals and so on,” he explains. “They can only do it if the manufacturing facilities meet the most stringent cost and efficiency requirements.”
Those requirements were among the topics looked at in a recent Factory 5.0 workshop hosted by Analog Devices. “It went into a fair amount of detail on what Factory 5.0 will look like, the improved sustainability, reduced waste, faster time to market, and much else besides.”
Value chain
Another area of focus is on primary and secondary value chain activity. Primary value chain activities include manufacturing operations, supply chain, marketing and sales, and service. Secondary or support activities include company infrastructure, human resources management and procurement.
“That’s what we are doing at the moment,” says Moran. “It’s very exciting. We believe it will make a big contribution to sustaining the sector into the future. It’s an imperative to have now. It’s about continuously moving up the value chain. Many of these companies are part of large global networks where they are competing with other companies in their groups for new investments and manufacturing mandates. We hope that these companies will be exemplar sites in their groups. We want the Irish sector to be best in class in the world for this type of activity. We have made a very good beginning with this group of companies. They are all very motivated and are putting time and resources into it.”
And there are benefits from indigenous industry as well. “A platform is being built for potential suppliers to go in to pitch for new business opportunities. The ecosystem will also enable collaboration on research projects as well as the sharing of best practice. For example, on the sustainability side that could be reusing solvents. How can that be done? What are the regulatory hurdles involved? On energy and resource efficiency, we can look at taking paper out of the operation and digitising it. We will go on to look at skills requirements and training.”
Looking to the future, he says the group is now ready to take the project to the next stage. “We have defined our north star where the biopharma value chain enabled by Ireland’s partnership ecosystem can deliver transformational Factory 5.0 benefits.”